

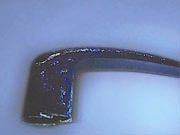
![Figure 3: The powdered metal part at lower left was impregnated with IMPCO’s PoreSeal resin and Surface Matrix Sealing™ processing prior to plating. The part at upper right was not impregnated — note the corrosion in the form of black spots. [Photo courtesy of Anoplate Corporation, Syracuse, N.Y.]](/media/aazjiip1/f10e7f94-e721-40a1-ad1b-e69a31b60142.jpg)

![Figure 4b
Figure 4a and 4b: Typical results for impregnated vs. un-impregnated anodized aluminum heat sinks. [Photos courtesy of Anoplate Corporation, Syracuse, N.Y.]](/media/vb5d4wby/0d5df86a-8895-4f0e-8a82-316907ccab4f.jpg)
![Figure 5: The two brass-plated handles above were subjected to a continuous salt-spray test for 96 hours at 95% humidity and 95° F. The handle on the left had not been impregnated and exhibited porosity-associated corrosion failure in less than 24 hours. The handle on the right was Surface Matrix Sealing™ pre-processed and showed no corrosion after 96 hours. [Photo courtesy of Imtech of California, Santa Fe Springs, Calif., and Quaker City Plating, Whittier, Calif.]](/media/bj4bbasr/d77cc1c2-7f7a-4cca-bc85-3878cab2edeb.jpg)
For those in the business of finishing decorative parts, it is no secret that high part rejection rates caused by unacceptable end-product finishes, which are the result of porosity, cut deeply into profits. At IMPCO we have developed proven, inexpensive, proprietary impregnating protocols that we term Surface Matrix Sealing™ (SMS), which when used as a pre-process to anodizing, plating, or coating can dramatically increase profitability by reducing finishing rejection rates. Succinctly said, by improving the “looks,” by preventing the “leaks” we lower the cost and, more importantly, increase profits. Better finishes equal better bottom lines.
It’s All About the Money As metal parts make their way from fabrication to end product, their value increases at every step, especially in the finishing processes. Consequently, rejection of parts late in the production cycle due to poor finishes, such as spotting and bleedout, costs much more than rejection in an “as-cast” state. Why? For castings, re-melting, while costly, allows the caster to reproduce the parts for little more than the cost of energy. With weldments or brazed assemblies, the same is true: returning to the previous step is economically possible. At the next step of the production process—machining—scrapping parts is a bigger loss, but since the metal is still pure and can be reused easily, the base material cost is recovered when the parts are remanufactured. Though losses are compounded by adding the machining costs to the re-melt cost, they are manageable.
As parts move beyond manufacturing to finishing, it’s an entirely different story. Additional finishing costs (labor, materials, energy, etc.) invested in a run of parts are completely lost when parts are discarded after unsuccessful finishing. These costs (for polishing, plating, cleaning, coating, etc.) are cumulative, and progressively more expensive as parts move toward completion. If parts have been polished, plated, coated, and then rejected, they become expensive scrap. Not only are the finishing expenses lost, but many times the scrap value of the base metal is substantially reduced (by half or more) because of “contaminants” in the form of coatings, introduced in finishing. Even if the plating or coating is removed in an effort to enhance the scrap value, the cost of “stripping” is roughly the same as the cost of application, and generally not recovered. As with all quality problems, the upward cost spiral continues—more rejected parts require more parts to be made and finished, resulting in more costs incurred.
What Causes the Majority of Rejections? A significant number of finishing problems are porosity-related. All castings and powdered metal parts are porous. Even weldments or brazed fabrications have porosity inclusions in their seams. During machining and finishing, pores can collect water, solvents, acids, and oils. Later, collected contaminants can leach to the finished surface, manifested as corrosion, pitting, or spotting, ruining both the functional and decorative purposes of the part. Engineers know of the problems associated with porosity and the solutions; they know how to change the part’s design and other parameters in order to reduce porosity. But these singular efforts to reduce porosity rejection rates can be costly and time-consuming, and though they may solve functional problems, decorative issues can persist.
As metal finishers have learned, part design changes or process modifications, while helpful, do not always solve the problem. Relocating a runner or riser or changing seam patterns or brazed joints only go so far. While it is true that advanced manufacturing techniques can reduce pore sizes to a nano scale, even these size reductions do not solve the bigger problem encountered for decorative parts: surface blemishes. Indeed, for the finisher, the smaller the porosity, the more difficult it is to deal with imperfections and prepare a part for a decorative finish.
Experience has shown that finishers’ reliance on the primary manufacturers to solve porosity problems is risky. Generally, manufacturing solutions involve individually re-engineering the part, its design, or the process—any of which increases costs. With the product lines of a single manufacturer encompassing hundreds of different parts, each with its production requirements, redesigning them all individually is extremely time-consuming, expensive, and impractical. With all the variables involved, the uncontrollable ones can overwhelm the controllable, and porosity-associated problems can reappear.
Sadly, many finishing houses have found that high rejection rates are the norm and have simply incorporated the costs into the system. However, with new developments in porosity sealing, the economics have changed. In the vast majority of cases, an inexpensive global solution to the porosity problem is available—Surface Matrix Sealing™ using vacuum/pressure impregnation with uniquely engineered impregnants and matching process protocols to fill porosity and provide the necessary integrity to a part’s pre-finished surface.
Profit Impact Because value is added at each consecutive step of a part’s post-casting process, rejection hurts most when it comes during or after finishing. Figure 1 shows the impact of rejected parts on profits, using actual data. As can be clearly seen, the impact of a high rejection rate on profitability can be tremendous. The entire cost of parts processed has to be borne by those deemed successful. Because impregnation takes place prior to finishing, it basically rescues parts that would otherwise have been rejected, thereby dramatically lowering the rejection rate. And because the costs associated with impregnation are minimal, profits can jump dramatically. |
Art vs. Science Some say that the part manufacturing process is science combined with art, while others maintain that finishing is more art than science. From the manufacturers’ point of view, post-cast finishing operations, such as plating, anodizing or coating, are but one consideration in the profit cycle. Generally, their primary “finishing” operations are machining and joining, and these are all about the science of dimensional tolerances that are immediately measurable and controllable. They know, however, that final finishing, the bright new look resulting from polishing, plating, anodizing, painting, etc., often masks flaws that take time to present themselves. Bleedout, spotting, cracks, blisters, and other problems can ruin a part that looked fine immediately after finishing, with the flaws appearing hours or weeks later. Early finishing successes can become costly market and reputation failures, unseen with inspections and appearing only after assembly and shipment [Figures 2–5].
Casting, Conventional vs. Decorative The First “L”: Leakers Casting technologies have always focused on controlling porosity, with a mindset to eliminate porosity that would cause a part to leak when used under pressure, such as in engines, pumps, or many other common industrial applications. For impregnators, in their traditional role of dealing with leakers, as long as a porosity pathway is sealed somewhere along its length, the part is acceptable. Therefore, with pressure tightness the measure of success, impregnators have developed materials and processing to meet that need. By combining modern impregnation processes with new casting technologies, leakers have now been reduced to the level of a minor annoyance. Similarly, for other manufactured parts modern machining, automated design, and special attention to form and fit have reduced weldment and brazing porosity leakage problems to a minimum.
The Other “L”: Looks With decorative parts, it’s all about looks. A metal finishing house that processes building hardware, for example, will have a whole different set of concerns than a valve company. Attention to surface imperfections replaces concerns about the physical integrity of the part from the start. The problems of porosity can be further complicated if machining or polishing a part opens up formerly enclosed porosity. Polishing may even smear a very thin layer of metal flake over porosity, temporarily masking it until later, when polishing compounds or acids used in plating operations bleed back out. Finally, heat-curing in coating processes can cause surfaces to bubble and smears to break from entrained liquids that boil out and erupt. The “First ‘L’ Leakers,” although successfully pressure-tight, become rejects because the porosity is not totally filled, thus allowing residually entrained finishing contaminants to corrode and discolor the part’s finish from deep below the surface.
More About Porosity Porosity imperfections in castings, weldments, and brazings are a fact of life. Porosity generally occurs in weldments and brazings at the seam. All castings, weldments, and brazings can be porous — the unavoidable consequence of one or more of the following:
Porosity manifests itself in different ways and can be classified as continuous, blind, or totally enclosed. Sometimes cracking or checking can look and act like porosity to metal finishers.
|
The Secrets of Surface Matrix Sealing™ For a successful decorative finish, a part must have true surface integrity. The real challenge with porosity is not to just plug the pore, but to fully fill it up to the part’s surface, leaving no place where contaminants can remain. To meet this more stringent requirement, IMPCO re-engineered the dynamics of the process, reformulated materials, and greatly improved process control. We call these procedures Surface Matrix Sealing™.
As previously mentioned, water, acids, solvents, machining fluids, and other contaminants are often trapped in porosity, only to bleed out after the part has been coated. Research indicates that water, at its normal surface tension of 65–70 dynes/cm², cannot easily penetrate porosity with an opening smaller than 65µm. But by adding surfactants, oils (for cutting and lubricity in machine operations), or heat (from various operations) to water, a reduction in surface tension occurs, thereby easing the contaminant’s entry into even the smallest pore. There it remains, held by capillary forces until other physical changes, such as corrosion, bleedout, or heat-associated eruptions occur.
To address these process issues, IMPCO employed a multi-phase approach using unique, airless cleaning techniques and re-engineered the impregnation materials and process. Finishers know that a clean surface is critical for high-quality coatings. However, since most cleaning operations are water-based, the physical difficulties and limitations of water play an important role, especially since porosity is effectively an extension of the part’s surface area. Using the cleaning triad of heat, chemistry, and force, an effective pore-cleaning technique is an important contributor to full-fill impregnation. Utilizing this understanding, IMPCO developed new processing techniques to address pore contamination.
The second development phase was to address the differences between traditional sealed parts and finishers’ requirements for fully filling the porosity up to the part surface.
For those not familiar with “full-fill” impregnation, parts to be sealed are placed in a vacuum chamber to remove all entrained air from porosity. A low dynamic viscosity resin is introduced while the parts are still under vacuum. Applied external pressure, aided by capillary forces, then pushes the sealant into the porosity, completely filling the voids. Once impregnated, the part’s surface is carefully washed to remove resin from it, but not from the porosity. The resin in the porosity is solidified, resulting in a completely sealed pore that will not allow contaminant entry and subsequent bleedout.
To fully fill porosity, properly formulated impregnants (resins) are required. With surface tensions less than half that of water and low dynamic viscosities, traditional impregnation resins can enter and fill all voids. However, retaining the resin in the porosity presented a different challenge. From the industry point of view, good penetration and surface “wash-ability” of the resin commanded a premium, so impregnants were engineered for easy removal in water. However, good “wash-ability” also means difficulty in retaining a high volume of resin in the porosity, encouraging a portion of the resin to “bleed out.”
To improve retention, IMPCO addressed the bleed-out issues in reverse. Understanding and utilizing the dynamic forces to clean porosity prior to impregnation, we developed resins that utilize these same forces to remain in the porosity, while still allowing any excess resin that clings to the part’s surface to be easily removed in the impregnation washing step. The results are parts that have a clean and fully sealed surface as a base for plating, anodizing, or coating without porosity-related defects.
Earlier we described the challenges faced in plating on a porous surface. For anodizing and other conversion coatings, porosity can even contribute to a thinning of the coating and cause smutting or powdering, resulting in substantially diminished corrosion protection. Here, increased coating thickness corresponds to better corrosion resistance. Since these anodic coatings result from the chemical reaction promoted by electricity between the metal surface and the acid bath, an uneven surface with deep pores requires prolonged processing to achieve the desired coating thickness. The unintended result of this lengthened time is the degradation of the oxide, resulting in a soft, powdery surface with diminished corrosion resistance or inconsistent and unacceptable visual results.
Utilizing our enhanced impregnation techniques prior to anodizing solves this problem. It fills the pores, thus preventing the entry of other corrosion-causing contamination, and it provides a better base on which to build the full anodized-coating thickness on a uniform basis, thus improving both visual and physical results.
Applied coatings also have related porosity problems. Again, contaminants, generally in the form of water-based cleaners, are sucked into the porosity–like voids. The parts are coated and progress to the heat cure stage. During heat cure, the coatings begin to flow, level, and crosslink. They effectively form a vapor-tight seal for the water entrained in the porosity, and creating an enclosed vessel. As the part temperature increases to the 300–350° (150–175°C) final cure temperature, moisture vaporizes, producing enough internal pressure (50–120 psig/3.5–8.3 bar) to erupt through the partially cured coating surface, causing a crack, flake, fissure, or blister that will prevent good coating adhesion.
The bottom line is that a flawed decorative part cannot be sold. Either the finisher gets the blame and suffers the loss or, if it is an in-house operation, the increased costs need to be accounted for accurately. In the end, looks suffer and lots of money is needlessly spent.
For manufacturers and finishers of decorative parts, it is time for IMPCO’s SMS protocols to become an integral part of the manufacturing process. With this system, a finishing operation can show dramatic increases in productivity and profits because part quality is ensured and the number of rejects is reduced. Although the cost of impregnation varies by application, it usually ranges from 1–5% of a part’s finished cost, and contributes directly to profits by reducing rejections.
Coatings Coatings for cast parts can be classified as deposit, applied, or conversion coatings:
|
Seek Out the Experts Though sometimes seen as a simple process, impregnation for decorative finishing is more complex and demanding than it is for solving parts’ leakage problems. Incorrectly engineered materials and improper methods can force resin out of a pore before it has fully cured, basically undoing the “full fill.” Incompletely cured resin can damage a decorative finish by adhering to the casting’s surface and preventing the bond between the base metal and the coating.
During the impregnation process itself, careful attention to temperature and pressure can optimize the results. For example, traditional casting impregnation resin is formulated to cure in water to a hard, durable thermoset plastic impervious to acids and alkalis and resistant to high heat. However, where moisture is a contamination contributor and the same resin is cured in an oven, cure times lengthen. Inadequate heat/soak time will prevent the resins from fully curing, and subsequent surface finishing will suffer. Other important parameters—vacuum cycles, soak cycles, pressure cycles, heating cycles, and rinse cycles—can all be modified as needed to achieve “full fill.”
Conclusion For the decorative finishes of castings, weldments or brazings, the proper vacuum resin impregnation method saves money immediately. For maximum profitability in the finishing of decorative metal parts, it is time for the IMPCO Surface Matrix Sealing™ impregnating processes to become standard procedure and successfully produce the decorative looks without the cost of the rejects.
While a finisher will notice the lower reject rates right away, SMS brings additional benefits that become apparent over time. For example, plating times and thickness usually can be reduced, thanks to fully filled porosity contributing to enhanced corrosion resistance. And with IMPCO’s attention to cleaning, more contaminants are removed prior to coating. Along with ”full fill” of porosity, this means the liquid “baths” for plating and other finishing processes will not have to be changed as often. In these and other ways, proper cleaning and impregnation make for a more efficient finishing operation, helping the shop to manage labor, time, and capacity while producing parts for less cost, more quickly, and to higher quality. In other words, “it’s all about the money!”
BIO Peter T. Gebhard is the Principal Investor in IMPCO Incorporated. IMPCO, with 60 years of experience in metal impregnation technology, offers cleaning, sealing, and leak-testing services in addition to proprietary sealing resins for impregnating cast parts, powdered-metal parts, and electronic connectors. Mr. Gebhard is also Chairman of Stoutheart Corporation, an investment firm specializing in metal manufacturing and finishing companies. For more information, contact Mr. Gebhard at IMPCO, Inc., 27 Dexter Road, East Providence, RI 02914, TEL: (401) 521-2490 or toll-free at 1-800-779-2491, FAX: (401) 521-5690, E-mail: mail@impco-inc.com, Web: www.impco-inc.com.